Serial number 001 in Vancouver | The success of craft beer today is down to the pioneering efforts of a handful of adventurous brewers. While some big breweries are now battling with a drop in sales, the upsurge of smaller brewing companies continues. One example of this is the rise of Steamworks Brewery from Vancouver in Canada which began long before the current craft beer boom. Early on in its career the company opted for systems from KHS which is also why the Canadians were recently able to enjoy a very special first: the arrival of the prototype of Innofill CAN C to manage can filling the Innofill Can C in Vancouver.
The Neutraubling-based manufacturer of filling and packaging technology released its annual report on 21 March 2019.
Krones continued to grow in 2018. Revenue increased by 4.4% to EUR 3.85 billion. The company thus attained the revised forecast of 4% revenue growth announced in autumn 2018. Adjusted for currency and acquisition effects, revenue in 2018 rose by around 5%.
Following the announcement of the partnership between Petainer, KHS Japan and Mitsubishi Chemical to bring one-way PET kegs to the Japanese beer market, the unique new DLC keg, 10 and 20l, has been launched in the market.
As a leading player in the domestic beer market, Heineken Vietnam was looking to significantly increase the beer production output of its Tien Giang site, located in the south of the country. And they needed to do it quickly. Long-term partner and expert in turnkey solutions for beer players, Gebo Cermex, supported this ambitious goal with a complete line project, featuring among other highly efficient and high-performing solutions the new Sidel filler, EvoFILL Can.
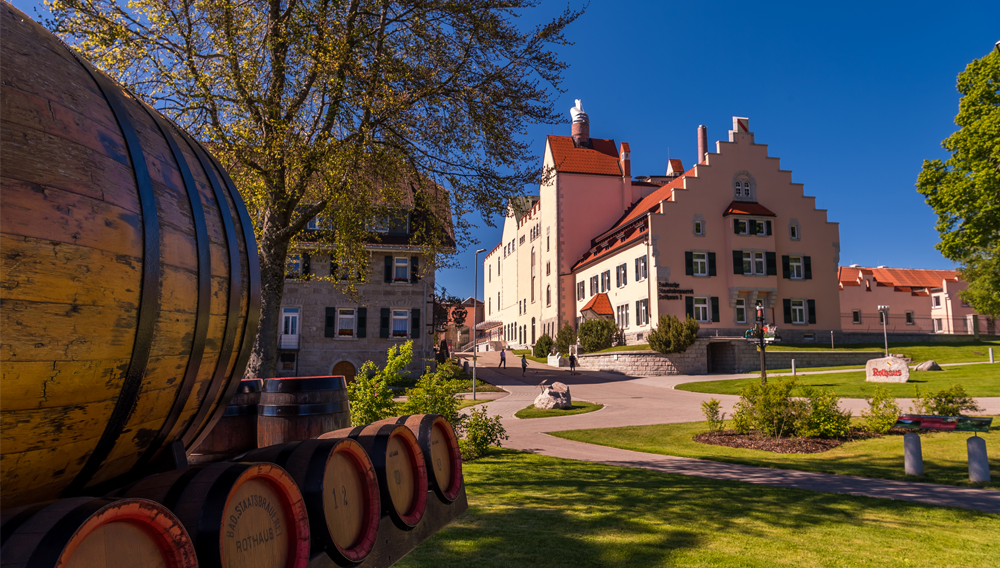
Increased line efficiency | The renowned German brewery Rothaus inaugurated state-of-the-art sorting and filling lines at their site in the High Black Forest in the beginning of the year. Maximum uptime and increased reliability of these lines were made possible thanks to the line engineering and conveying expertise of their longstanding business partner Gebo Cermex.
CO.MAC is an active company in the design, manufacturing, repair, maintenance and technical support for beverage filling and packaging machines, especially beer in returnable and non-returnable kegs.
The water company has invested in state-of-the-art technology to cater to increased demand for their products from both Ireland and the UK markets. This choice gave them both the flexibility to tackle strong market growth and the ability to handle new product launches.
The Silexa Growler&BottleFiller is a new innovation for small breweries and beer pubs. Per device up to four different beers in up to four different bottle sizes can be chosen. On a full-colour touch display, the filling process is explained in simple steps: First, choice of beer; second, choice of the desired growler that is then put into the device. A handling error is excluded, the device detects whether the right growler has been set. After lowering the lid, the filling process can be started; an adjustable RGB LED lighting highlights the scenery yet. Depending on the type of beer about two liters are filled in 60 seconds. The growler is given a CO2 blast so that it can be closed without oxygen occlusion, so beer is stable for at least two weeks, depending on the variety also four weeks.
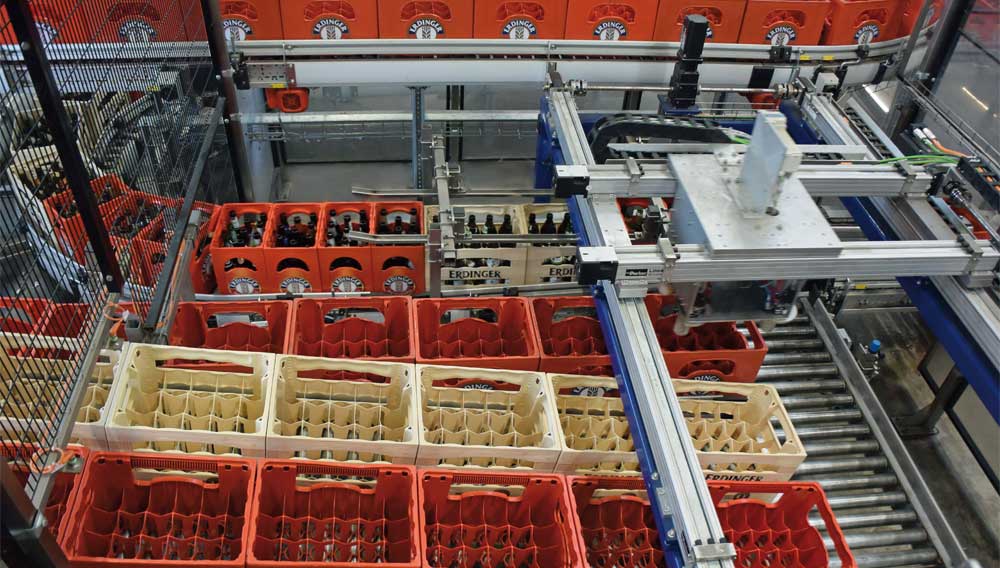
Homogeneous | In November 2017, the private brewery Erdinger Weißbräu Werner Brombach GmbH, Erding, Germany, inaugurated a new bottling line. The brewery also invested in a new central sorting facility, which ensures the supply of all three filling lines with pure empties.
Nanjing Ziquan, one of China’s leading co-packers, has turned again to to the Switzerland-based company to increase its hot fill production capacity of Mizone, a functional drink brand particularly popular in China and packaged in PET, for which consumption is growing. The new line – running at a speed of 36,000 bottles per hour (bph) – follows positive feedback on a similar complete hot fill PET line installed in 2013. It brings the total number of hot fill lines installed in the Nanjing plant to three. The Chinese co-packer were looking for a solution which was respecting the highest hygienic standards required by its customer, while paying close attention to cost-efficiency so to keep the positive trajectory of its profitability.
Current issue
Most Read
BRAUWELT on tour
Current issue
Most Read
BRAUWELT on tour
-
Hopsteiner
Optimization of kettle hopping prior to dealcoholization
-
Hopsteiner
Excellent digital Service: the Hopsteiner Customer Portal
-
Hopsteiner
Variations in hop aroma depending on crop year
-
Hopsteiner
Playing with tradition: Hopsteiner Hopoils - Type Hoptanical
-
Hopsteiner
Crop and market update & hop crop 2023 estimate